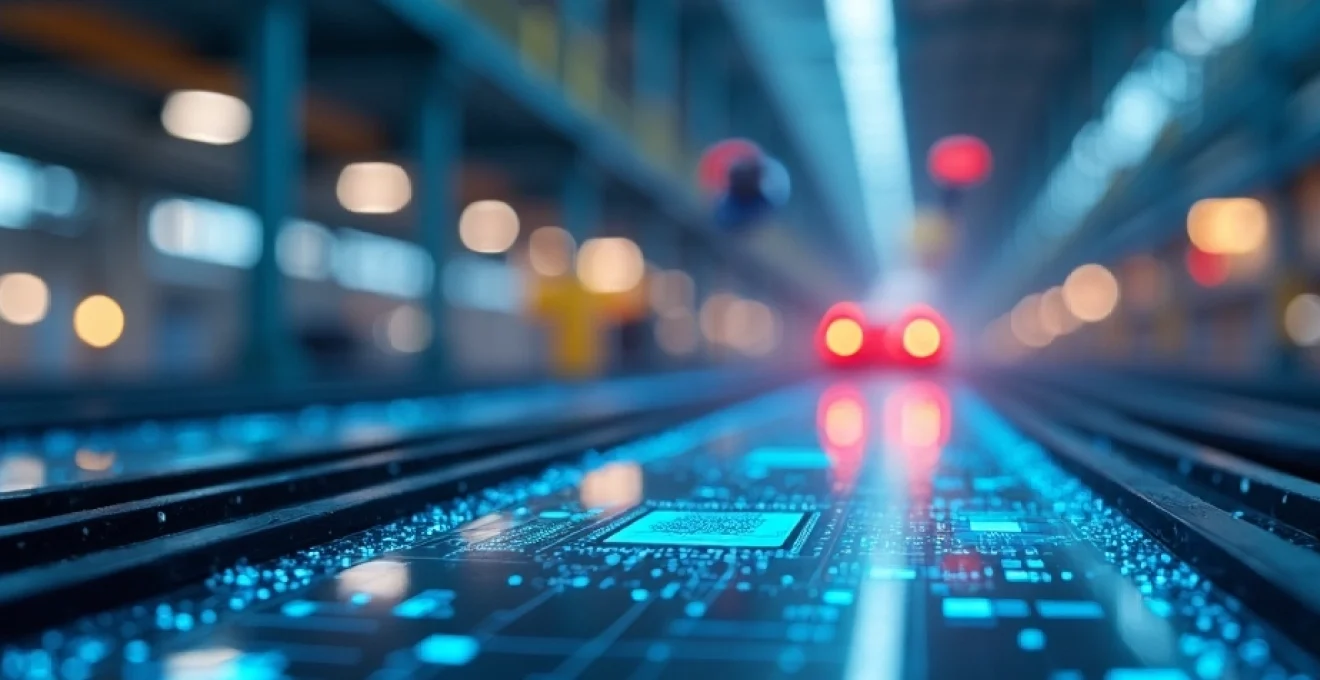
The industrial landscape is undergoing a radical transformation with the advent of intelligent production environments. These sophisticated systems are revolutionizing manufacturing processes, enhancing efficiency, and paving the way for unprecedented levels of automation and connectivity. By integrating cutting-edge technologies such as artificial intelligence, the Internet of Things (IoT), and cloud computing, factories are evolving into smart, adaptive ecosystems capable of self-optimization and real-time decision-making.
As we delve into the intricate architecture of these intelligent production environments, you'll discover how they're reshaping the manufacturing sector and driving Industry 4.0 forward. From the components that form the backbone of smart factories to the advanced algorithms powering predictive maintenance, this exploration will unveil the future of industrial production.
Smart factory components in intelligent production systems
At the heart of intelligent production environments lie the smart factory components that form the foundation of these advanced systems. These components work in harmony to create a seamless, interconnected production ecosystem that's responsive, efficient, and highly adaptable to changing demands.
One of the key elements in smart factories is the implementation of cyber-physical systems (CPS). These systems bridge the gap between the physical and digital worlds, allowing for real-time monitoring and control of production processes. Through a network of sensors, actuators, and control systems, CPS enables machines to communicate with each other and make autonomous decisions based on real-time data.
Another crucial component is the digital thread, which serves as a communication framework that connects data flows and integrates the various stages of the product lifecycle. This thread ensures that all stakeholders have access to the most up-to-date information, from design and engineering to manufacturing and maintenance.
Advanced robotics and automation systems play a pivotal role in smart factories. Collaborative robots, or cobots, work alongside human operators, enhancing productivity and safety. These robots are equipped with sophisticated sensors and AI algorithms that allow them to adapt to their environment and perform complex tasks with precision.
Industrial internet of things (IIoT) integration for real-time data flow
The Industrial Internet of Things (IIoT) is the backbone of intelligent production environments, enabling seamless connectivity and data exchange between machines, systems, and humans. By leveraging IIoT, manufacturers can achieve unprecedented levels of operational visibility, process optimization, and predictive capabilities.
MQTT protocol implementation for sensor communication
At the core of IIoT communication lies the MQTT
(Message Queuing Telemetry Transport) protocol. This lightweight messaging protocol is designed for high-latency or unreliable networks, making it ideal for sensor-to-cloud communication in industrial settings. MQTT's publish-subscribe model allows for efficient data distribution and real-time updates across the production environment.
OPC UA standards for machine-to-machine connectivity
OPC UA (Open Platform Communications Unified Architecture) is another critical standard in IIoT integration. This platform-independent protocol ensures interoperability between different industrial systems and devices. OPC UA provides a secure and reliable framework for data exchange, enabling seamless communication between diverse equipment and software applications in the smart factory ecosystem.
Edge computing devices for local data processing
To manage the vast amounts of data generated by IIoT devices, edge computing plays a crucial role in intelligent production environments. Edge devices process data locally, reducing latency and bandwidth usage while enabling real-time decision-making at the point of production. This distributed computing approach enhances system responsiveness and reliability, particularly in time-sensitive applications.
5G networks enabling low-latency data transmission
The rollout of 5G networks is set to revolutionize IIoT connectivity in smart factories. With its ultra-low latency and high-bandwidth capabilities, 5G enables near-instantaneous data transmission and supports a much higher density of connected devices. This technology will facilitate more sophisticated real-time control systems and enable new applications such as augmented reality for maintenance and training.
Artificial intelligence and machine learning in manufacturing processes
Artificial Intelligence (AI) and Machine Learning (ML) are transforming manufacturing processes, introducing unprecedented levels of automation, optimization, and predictive capabilities. These technologies are the driving force behind many of the intelligent features in modern production environments.
Predictive maintenance algorithms using vibration analysis
One of the most impactful applications of AI in manufacturing is predictive maintenance. By analyzing vibration patterns and other sensor data, machine learning algorithms can detect anomalies and predict equipment failures before they occur. This proactive approach significantly reduces downtime and maintenance costs, improving overall equipment effectiveness (OEE).
For example, a vibration sensor on a critical piece of machinery might detect subtle changes in its operation. The AI system, trained on historical data, can interpret these changes and predict that a bearing is likely to fail within the next 500 operating hours. This allows maintenance teams to schedule repairs during planned downtime, avoiding costly unplanned stoppages.
Computer vision systems for quality control inspection
Computer vision, powered by deep learning algorithms, is revolutionizing quality control in manufacturing. These systems can inspect products at speeds and levels of accuracy far beyond human capabilities. By analyzing images and video feeds in real-time, AI-driven quality control can detect defects, ensure proper assembly, and even sort products based on visual characteristics.
Advanced computer vision systems can identify defects as small as a fraction of a millimeter, ensuring that only products meeting the highest quality standards reach the customer.
Reinforcement learning for adaptive production scheduling
Reinforcement learning, a branch of machine learning, is being applied to optimize production scheduling in intelligent manufacturing environments. These algorithms can adapt to changing conditions in real-time, balancing factors such as order priority, resource availability, and energy consumption to create dynamic, efficient production schedules.
As the AI system learns from each production run, it continually refines its scheduling strategies, leading to ever-improving efficiency and responsiveness to market demands. This adaptive approach is particularly valuable in industries with complex supply chains or highly variable product mixes.
Natural language processing for voice-controlled machinery
Natural Language Processing (NLP) is making its way onto the factory floor, enabling voice-controlled machinery and hands-free operation. This technology allows operators to interact with complex equipment using simple voice commands, improving safety and efficiency, especially in environments where manual input might be challenging or time-consuming.
Voice-controlled systems can also facilitate better documentation and reporting. Operators can dictate notes or reports while performing tasks, ensuring more accurate and timely record-keeping without interrupting their workflow.
Cloud-based manufacturing execution systems (MES)
Cloud-based Manufacturing Execution Systems (MES) are central to the architecture of intelligent production environments. These systems provide a comprehensive platform for managing and optimizing production processes, offering real-time visibility and control across the entire manufacturing operation.
AWS IoT Greengrass for hybrid cloud-edge deployments
AWS IoT Greengrass is a powerful tool for implementing hybrid cloud-edge architectures in manufacturing environments. This service extends AWS capabilities to edge devices, allowing them to act locally on the data they generate while still leveraging the cloud for management, analytics, and storage.
With AWS IoT Greengrass, you can deploy machine learning models directly to edge devices, enabling real-time inference without the need for constant cloud connectivity. This approach is particularly valuable in scenarios where low latency is critical or where network connectivity may be intermittent.
Microsoft Azure IoT Hub for device management and security
Microsoft Azure IoT Hub offers a comprehensive solution for device management and security in intelligent production environments. This cloud-based service enables secure, bidirectional communication between IoT applications and the devices they manage, at scale.
Azure IoT Hub provides features such as device provisioning, authentication, and monitoring, ensuring that your IoT infrastructure remains secure and manageable as it grows. It also integrates seamlessly with other Azure services, allowing you to build sophisticated analytics and machine learning pipelines to derive insights from your IoT data.
Google Cloud IoT core for scalable data analytics
Google Cloud IoT Core provides a fully managed service for connecting and managing IoT devices at scale. When integrated into intelligent production environments, it offers powerful capabilities for data ingestion, processing, and analysis.
One of the key advantages of Google Cloud IoT Core is its seamless integration with Google's big data analytics and machine learning services. This allows manufacturers to easily implement advanced analytics on their IoT data, uncovering insights that can drive process improvements and innovation.
Digital twin technology for virtual factory simulation
Digital twin technology is revolutionizing the way manufacturers design, test, and optimize their production processes. By creating a virtual replica of the physical factory, complete with real-time data feeds from sensors and systems, digital twins enable unprecedented levels of simulation and analysis.
These virtual models allow you to:
- Simulate production scenarios without disrupting actual operations
- Optimize layouts and workflows in a risk-free virtual environment
- Predict maintenance needs and potential failures before they occur
- Train operators on new equipment or processes using realistic simulations
The power of digital twins lies in their ability to integrate data from multiple sources, including IoT sensors, historical performance records, and even external factors like supply chain data or weather conditions. This holistic view enables more accurate predictions and better decision-making across all aspects of production.
Digital twins are not just static models; they evolve alongside the physical factory, continuously updating to reflect changes and improvements in the real-world environment.
As digital twin technology advances, we're seeing the emergence of digital thread concepts, where the twin follows the product throughout its entire lifecycle, from design and production to use and eventual recycling. This comprehensive approach is setting new standards for product quality, sustainability, and customer service in manufacturing.
Cybersecurity measures in connected production environments
As intelligent production environments become increasingly connected, cybersecurity has emerged as a critical concern. The integration of IT (Information Technology) and OT (Operational Technology) systems in smart factories creates new vulnerabilities that must be addressed to protect sensitive data and ensure operational continuity.
Industrial firewalls and network segmentation strategies
Implementing robust industrial firewalls and network segmentation is crucial for securing intelligent production environments. Unlike traditional IT firewalls, industrial firewalls are designed to understand and protect against threats specific to industrial control systems and protocols.
Network segmentation involves dividing the factory network into smaller subnetworks, or segments, each with its own security controls. This approach limits the potential spread of a security breach and allows for more granular control over data access and flow. Key strategies include:
- Implementing demilitarized zones (DMZs) between IT and OT networks
- Using virtual LANs (VLANs) to isolate critical systems
- Employing physical network separation for highly sensitive areas
Secure authentication protocols for IoT devices
With the proliferation of IoT devices in smart factories, secure authentication becomes paramount. Implementing strong authentication protocols ensures that only authorized devices can connect to the network and access sensitive data or controls.
Best practices for IoT device authentication include:
- Using unique, complex passwords for each device
- Implementing two-factor authentication where possible
- Employing certificate-based authentication for machine-to-machine communication
- Regularly updating and rotating authentication credentials
Additionally, implementing a robust Identity and Access Management (IAM) system can help manage and monitor device identities and permissions across the entire production environment.
Blockchain integration for supply chain traceability
Blockchain technology is emerging as a powerful tool for enhancing supply chain security and traceability in intelligent production environments. By creating an immutable, distributed ledger of transactions and events, blockchain can provide end-to-end visibility and accountability across complex supply networks.
Key benefits of blockchain integration in manufacturing include:
- Enhanced transparency and traceability of raw materials and finished products
- Improved detection and prevention of counterfeit components
- Streamlined compliance and auditing processes
- Increased trust and collaboration among supply chain partners
As blockchain technology matures, we're seeing innovative applications such as smart contracts automating supplier agreements and payments, further enhancing the security and efficiency of manufacturing supply chains.
The architecture of intelligent production environments represents a paradigm shift in manufacturing, combining advanced technologies to create adaptable, efficient, and secure production systems. As these technologies continue to evolve, they promise to unlock new levels of productivity, quality, and innovation in the manufacturing sector. By embracing these intelligent solutions, manufacturers can position themselves at the forefront of the Industry 4.0 revolution, ready to meet the challenges and opportunities of the future.