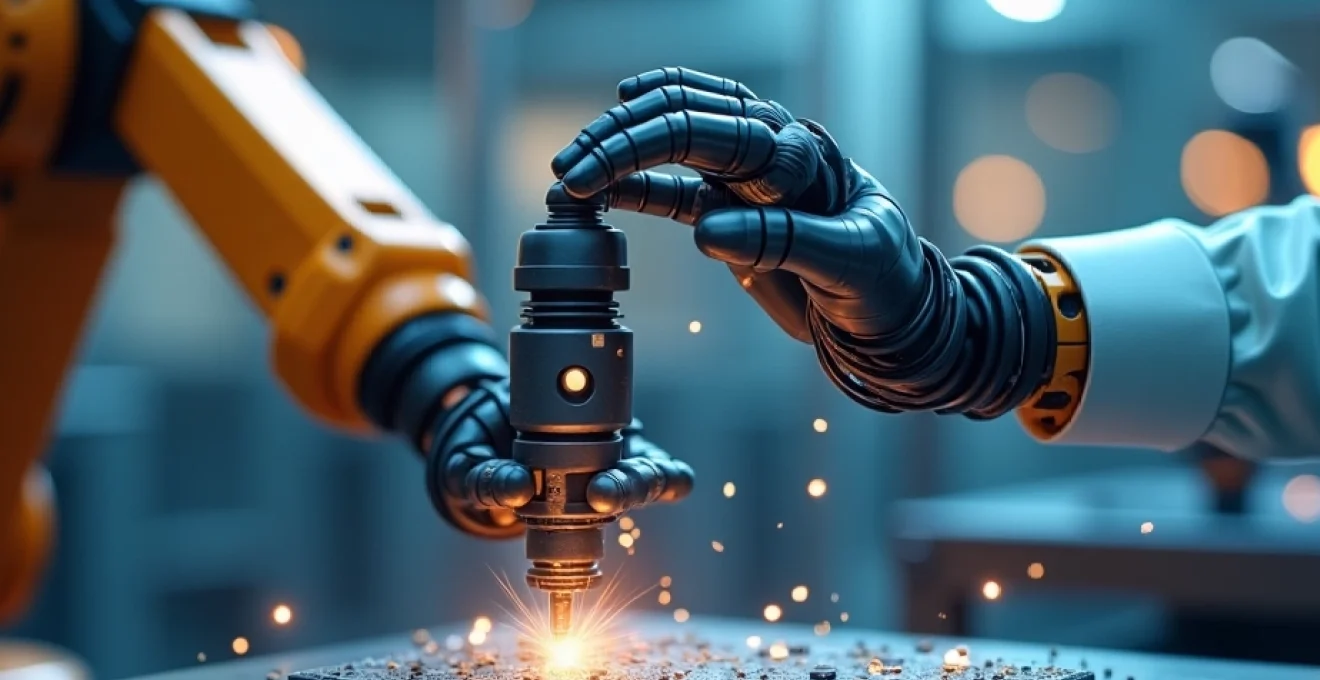
Industrial robots are transforming the manufacturing landscape, ushering in a new era of efficiency, precision, and productivity. These sophisticated machines are reshaping production lines, enhancing quality control, and enabling manufacturers to meet the ever-increasing demands of a global market. As automation technology continues to advance, the impact of industrial robots on manufacturing processes has become increasingly profound, offering solutions to long-standing challenges and opening up new possibilities for innovation.
Evolution of industrial robotics in manufacturing
The journey of industrial robotics in manufacturing has been marked by continuous innovation and adaptation. From the first rudimentary robotic arms introduced in the 1960s to today's highly advanced, AI-driven systems, the evolution has been nothing short of remarkable. Early robots were primarily used for simple, repetitive tasks such as welding and painting in automotive plants. However, as technology progressed, robots became more versatile, intelligent, and capable of handling complex operations across various industries.
One of the most significant developments in this evolution has been the integration of sensors and machine vision systems. These advancements have allowed robots to perceive their environment with unprecedented accuracy, enabling them to make real-time decisions and adjustments. This leap in capability has expanded the range of tasks robots can perform, from delicate assembly of electronic components to intricate surgical procedures in medical manufacturing.
Another pivotal moment in the evolution of industrial robotics was the introduction of collaborative robots, or cobots . These machines are designed to work alongside human operators safely, breaking down the traditional barriers between humans and robots on the factory floor. Cobots have opened up new possibilities for human-robot collaboration, combining the strength and precision of machines with the problem-solving skills and adaptability of human workers.
Key components and technologies of modern industrial robots
The capabilities of today's industrial robots are built upon a foundation of cutting-edge technologies and sophisticated components. Understanding these elements is crucial for grasping the full potential of robotic systems in manufacturing.
Advanced sensors and machine vision systems
Modern industrial robots are equipped with an array of sensors that act as their eyes and ears on the factory floor. These sensors include:
- Force-torque sensors for precise control of applied force
- Proximity sensors to detect nearby objects or humans
- Temperature sensors for monitoring operational conditions
- Acoustic sensors for quality control in processes like welding
Machine vision systems, powered by high-resolution cameras and sophisticated image processing algorithms, enable robots to inspect products, identify defects, and guide precision operations. This technology has revolutionized quality control processes, allowing for 100% inspection rates at speeds far exceeding human capabilities.
Sophisticated end effectors and gripping mechanisms
The end effector, often referred to as the robot's "hand," is a critical component that determines the tasks a robot can perform. Modern end effectors range from simple grippers to highly specialized tools designed for specific applications. Advancements in materials science and mechatronics have led to the development of adaptive grippers that can handle a wide variety of objects with varying shapes, sizes, and fragility levels.
For instance, some grippers now incorporate soft robotics principles, using flexible materials that can conform to the shape of objects, allowing for gentle handling of delicate items. Others use vacuum technology or electrostatic adhesion for handling materials that are difficult to grasp with traditional methods.
Artificial intelligence and machine learning integration
The integration of artificial intelligence (AI) and machine learning (ML) has been a game-changer for industrial robotics. These technologies enable robots to learn from experience, adapt to new situations, and even predict maintenance needs before failures occur. AI-powered robots can optimize their own movements, reducing energy consumption and wear while increasing efficiency.
Machine learning algorithms allow robots to improve their performance over time by analyzing vast amounts of data collected during operations. This capability is particularly valuable in complex manufacturing environments where conditions can change rapidly, requiring quick adjustments to maintain productivity and quality.
Collaborative robot (cobot) innovations
Collaborative robots represent a significant leap forward in human-robot interaction. Unlike traditional industrial robots that operate in isolated areas, cobots are designed to work safely alongside human workers. They incorporate several innovative features:
- Force-limiting technology that stops the robot upon contact with humans
- Lightweight, rounded designs to minimize injury risk
- Intuitive programming interfaces for easy setup and reprogramming
- Advanced vision systems for real-time environment awareness
These innovations have made cobots particularly valuable in small to medium-sized enterprises (SMEs) where flexibility and ease of use are crucial. Cobots can be easily redeployed to different tasks, making them ideal for manufacturers with diverse product lines or frequent changeovers.
Impact of industrial robots on production efficiency
The adoption of industrial robots has led to significant improvements in manufacturing efficiency across various sectors. Let's explore the key areas where robots are making a substantial impact.
Increased throughput and cycle time reduction
Industrial robots can operate at speeds and precision levels that far exceed human capabilities. This translates to dramatically increased production rates and reduced cycle times. For example, in automotive manufacturing, robots can perform welding operations up to five times faster than manual welders, with consistent quality across all welds.
Moreover, robots don't require breaks or shifts, allowing for 24/7 operation in many cases. This continuous production capability can significantly boost overall output, especially in industries with high demand or tight production schedules.
Quality control and defect minimization
Robotic systems equipped with advanced vision and sensor technologies can perform 100% inspection of products, detecting even microscopic defects that might be missed by human inspectors. This level of scrutiny ensures higher product quality and reduces the likelihood of defective items reaching customers.
In industries such as electronics manufacturing, where components are becoming increasingly smaller and more complex, robotic inspection systems have become indispensable. They can inspect thousands of solder joints on a printed circuit board in seconds, identifying issues that would be virtually impossible for a human to detect reliably.
24/7 operation capabilities
One of the most significant advantages of industrial robots is their ability to operate continuously without fatigue. This 24/7 operation capability allows manufacturers to maximize production output and meet tight deadlines. In industries with high energy costs, running operations during off-peak hours can also lead to significant cost savings.
Continuous operation is particularly valuable in processes that require consistent conditions, such as certain chemical reactions or material curing processes. Robots can maintain precise control over these processes without the variability introduced by human operators changing shifts.
Flexible manufacturing and quick retooling
Modern industrial robots are highly adaptable and can be quickly reprogrammed for different tasks. This flexibility is crucial in today's manufacturing environment, where product lifecycles are shortening, and consumer demand for customization is increasing.
For instance, an automotive assembly line equipped with flexible robotic systems can switch between different car models with minimal downtime. This ability to quickly retool allows manufacturers to respond rapidly to market changes and maintain a competitive edge.
Industrial robot applications across manufacturing sectors
The versatility of industrial robots has led to their widespread adoption across various manufacturing sectors. Let's examine some specific applications in key industries.
Automotive assembly and welding processes
The automotive industry has been at the forefront of robot adoption since the 1960s. Today, robots are integral to nearly every aspect of car manufacturing, from body assembly to painting and final inspection. Robotic welding systems, in particular, have revolutionized automotive production, offering precision and consistency that surpass human capabilities.
Advanced robotic systems in automotive plants can perform complex tasks such as applying sealants, installing windshields, and even conduct final quality checks using machine vision. These applications have not only improved product quality but also significantly reduced production times and costs.
Electronics PCB manufacturing and testing
In the electronics industry, robots play a crucial role in the production of printed circuit boards (PCBs). Robotic systems are used for precise component placement, soldering, and inspection. The miniaturization of electronic components has made human assembly increasingly challenging, if not impossible in some cases.
Robots equipped with high-precision vision systems can place thousands of components per hour with micron-level accuracy. They can also perform automated optical inspection (AOI) to detect defects such as misaligned components or solder bridging, ensuring the quality and reliability of electronic products.
Pharmaceutical packaging and handling
The pharmaceutical industry relies heavily on robotic systems for packaging and handling of medications. Robots ensure precise dosing, sterile handling, and accurate labeling of pharmaceutical products. In cleanroom environments, robots can operate without the risk of human contamination, maintaining the strict hygiene standards required in drug manufacturing.
Robotic systems are also used in drug discovery processes, where they can perform high-throughput screening of potential drug compounds. These applications significantly accelerate the drug development process while reducing the risk of human error.
Food processing and packaging automation
In the food industry, robots are increasingly used for tasks ranging from sorting and grading produce to packaging finished products. Robotic systems can handle delicate items like fruits and vegetables without damage, and their speed and precision lead to significant increases in processing efficiency.
For example, robotic pick-and-place systems can sort and package bakery items at rates far exceeding human capabilities. In meat processing, robots equipped with vision systems and specialized cutting tools can perform precise cuts, maximizing yield and ensuring consistent portion sizes.
Economic implications of industrial robot adoption
The widespread adoption of industrial robots has far-reaching economic implications for manufacturers and the broader economy. While the initial investment in robotic systems can be substantial, the long-term benefits often justify the cost.
One of the most significant economic impacts is the increase in productivity. Robots can work faster and longer than human workers, leading to higher output per unit of time. This increased productivity can translate into lower production costs, making manufacturers more competitive in global markets.
However, the adoption of robots also raises questions about job displacement. While some jobs may be automated, the implementation of robotic systems often creates new roles in robot operation, maintenance, and programming. This shift in job requirements underscores the need for workforce training and education to prepare workers for the changing manufacturing landscape.
Additionally, the use of robots can lead to improved product quality and consistency, which can enhance a company's reputation and potentially increase market share. The ability to produce high-quality goods at competitive prices can also open up new market opportunities, both domestically and internationally.
Future trends and challenges in industrial robotics
As we look to the future of industrial robotics, several emerging trends and challenges are shaping the field. Understanding these developments is crucial for manufacturers seeking to stay competitive in an increasingly automated world.
5G integration and industrial internet of things (IIoT)
The rollout of 5G networks promises to revolutionize industrial robotics by enabling faster, more reliable communication between robots, sensors, and control systems. This high-speed connectivity will facilitate the implementation of the Industrial Internet of Things (IIoT), where vast networks of interconnected devices can share data and coordinate actions in real-time.
5G's low latency and high bandwidth will enable more sophisticated remote operation of robots, potentially allowing experts to control and troubleshoot systems from anywhere in the world. This capability could be particularly valuable in hazardous environments or during global crises where on-site access is limited.
Human-robot collaboration and safety protocols
As collaborative robots become more prevalent, the development of advanced safety protocols and standards will be crucial. Future systems will likely incorporate more sophisticated sensors and AI algorithms to predict and prevent potential collisions or unsafe interactions between humans and robots.
Research is ongoing into intuitive interfaces that allow human workers to communicate with robots more naturally, potentially using gestures or voice commands. These developments aim to make human-robot collaboration more seamless and efficient, leveraging the strengths of both humans and machines.
Sustainable manufacturing with Energy-Efficient robots
As environmental concerns become increasingly pressing, the focus on developing energy-efficient robotic systems is growing. Future robots will likely incorporate more lightweight materials and energy-recuperation systems to minimize power consumption. Additionally, AI-driven optimization algorithms will help robots perform tasks with minimal energy expenditure.
The use of robots can also contribute to more sustainable manufacturing practices by reducing material waste through precise operations and optimized resource utilization. As manufacturers strive to meet sustainability goals, the role of robotics in achieving these objectives will become increasingly important.
Advancements in robot programming and ease of use
One of the challenges in widespread robot adoption, particularly among smaller manufacturers, has been the complexity of programming and integration. Future trends point towards more intuitive programming interfaces, potentially leveraging augmented reality (AR) for visual programming or natural language processing for voice-based instructions.
The development of no-code or low-code platforms for robot programming could democratize access to robotics technology, allowing even non-technical staff to configure and deploy robotic systems. This trend could significantly lower the barrier to entry for robotics adoption across various industries.
As industrial robots continue to evolve, they will undoubtedly play an increasingly central role in shaping the future of manufacturing. From enhancing productivity and quality to enabling new levels of customization and sustainability, the impact of robotics on the manufacturing sector is profound and far-reaching. Manufacturers who embrace these technologies and adapt to the changing landscape will be well-positioned to thrive in the increasingly automated and competitive global marketplace.