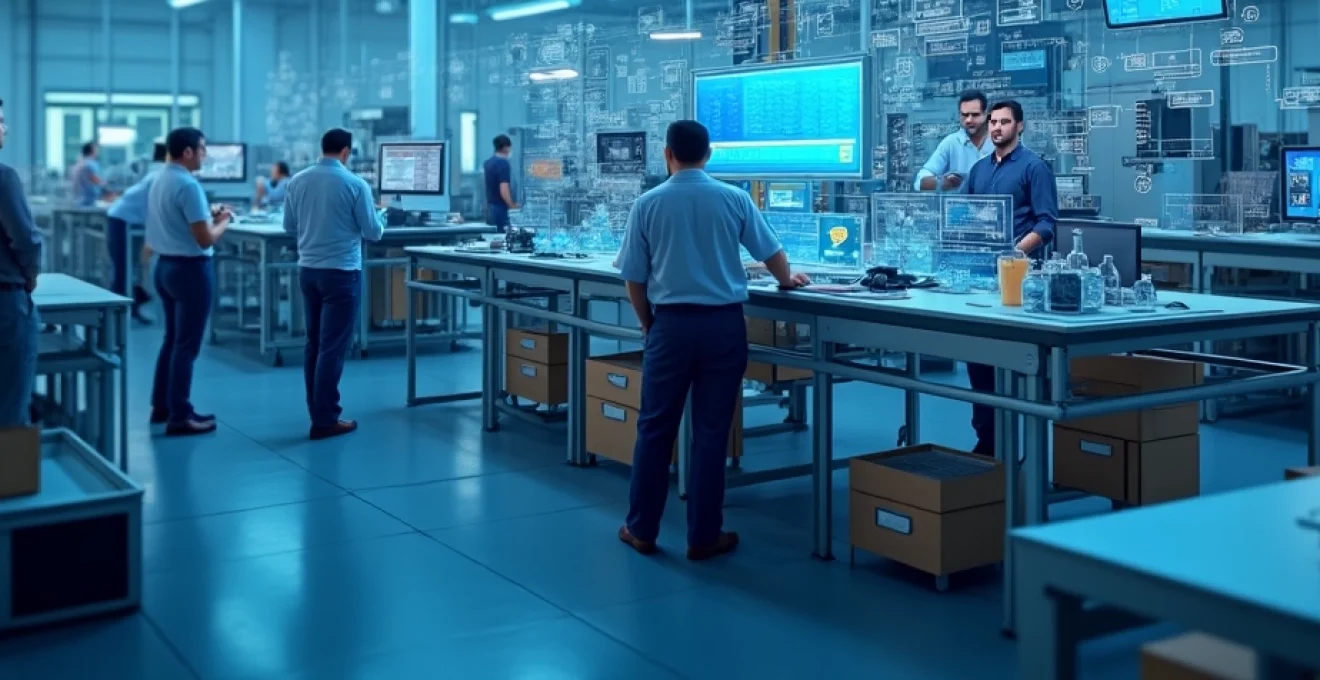
The concept of a connected factory represents a significant leap forward in manufacturing technology, revolutionizing how production facilities operate in the digital age. By seamlessly integrating advanced technologies, data analytics, and interconnected systems, connected factories are reshaping the industrial landscape. This innovative approach to manufacturing promises enhanced efficiency, improved quality control, and unprecedented levels of automation.
At its core, a connected factory leverages cutting-edge technologies to create a highly responsive and adaptive production environment. By harnessing the power of real-time data and intelligent systems, these factories can optimize processes, predict maintenance needs, and respond swiftly to changing market demands. This level of connectivity and intelligence is transforming traditional manufacturing paradigms, paving the way for more agile and competitive industrial operations.
Key components of connected factories
Connected factories rely on a sophisticated ecosystem of technologies working in harmony to create a smart, responsive manufacturing environment. These key components form the backbone of the connected factory, enabling seamless communication, data analysis, and process optimization across the entire production chain.
Industrial internet of things (IIoT) devices
At the heart of every connected factory lies a network of Industrial Internet of Things (IIoT) devices. These smart sensors and actuators are the eyes and ears of the factory floor, constantly collecting and transmitting data about every aspect of the production process. From monitoring machine performance to tracking inventory levels, IIoT devices provide the raw data that powers the intelligence of connected factories.
IIoT devices come in various forms, each tailored to specific manufacturing needs. For example, vibration sensors can detect early signs of machine wear, while temperature sensors ensure optimal operating conditions for sensitive equipment. By deploying a diverse array of IIoT devices, factories can create a comprehensive digital representation of their physical operations, often referred to as a digital twin.
Cloud computing platforms for data management
The vast amount of data generated by IIoT devices requires robust storage and processing capabilities. This is where cloud computing platforms play a crucial role in connected factories. These platforms offer scalable, flexible solutions for managing the enormous volumes of data flowing from the factory floor.
Cloud-based systems not only store data but also provide the computational power needed for complex analytics and machine learning algorithms. This enables manufacturers to gain deeper insights into their operations, identify patterns, and make data-driven decisions in real-time. Moreover, cloud platforms facilitate seamless integration with other enterprise systems, creating a unified view of the entire manufacturing ecosystem.
Advanced analytics tools for optimization
The true power of connected factories lies in their ability to transform raw data into actionable insights. Advanced analytics tools, powered by artificial intelligence and machine learning, sift through the massive datasets to uncover valuable patterns and opportunities for optimization.
These tools can predict equipment failures before they occur, optimize production schedules based on real-time demand, and even suggest improvements to product designs based on performance data. By leveraging advanced analytics, connected factories can achieve unprecedented levels of efficiency and quality control, staying ahead in an increasingly competitive global market.
Data collection processes in connected manufacturing
The lifeblood of any connected factory is data. The processes by which this data is collected, transmitted, and analyzed form the foundation of smart manufacturing. In a connected factory, data collection is a continuous, automated process that captures information from every corner of the production environment.
Data collection in connected manufacturing goes far beyond traditional methods. It's not just about recording production numbers or tracking inventory levels. Modern data collection processes in connected factories capture a wide range of parameters, from the micro-vibrations of a machine spindle to the exact temperature and humidity conditions on the factory floor. This granular level of data provides a complete picture of the manufacturing process, enabling precise control and optimization.
One of the key advantages of data collection in connected factories is its real-time nature. Unlike traditional manufacturing environments where data might be collected and analyzed at set intervals, connected factories continuously stream data from all connected devices. This real-time data flow allows for immediate response to any issues or opportunities that arise during production.
Real-time monitoring systems for production lines
Real-time monitoring systems are the nerve centers of connected factories, providing up-to-the-second insights into every aspect of the production process. These systems aggregate data from various sources across the factory floor, presenting it in intuitive dashboards that allow operators and managers to grasp the state of production at a glance.
Sensors tracking machine performance metrics
A critical component of real-time monitoring systems is the network of sensors tracking machine performance metrics. These sensors are attached to key points on manufacturing equipment, continuously measuring parameters such as temperature, vibration, power consumption, and operational speed.
By monitoring these metrics in real-time, factories can detect subtle changes in machine performance that might indicate impending failures or inefficiencies. For instance, an increase in vibration levels might suggest that a bearing is wearing out, allowing maintenance teams to schedule repairs before a catastrophic failure occurs. This predictive approach to maintenance can significantly reduce downtime and extend the lifespan of expensive manufacturing equipment.
Cameras detecting product quality issues
Advanced vision systems equipped with high-resolution cameras play a crucial role in maintaining product quality in connected factories. These cameras, often aided by sophisticated image processing algorithms, can detect even the slightest defects or inconsistencies in products as they move along the production line.
The ability to spot quality issues in real-time allows for immediate corrective action, reducing waste and ensuring that only products meeting the highest standards reach customers. Moreover, by analyzing patterns in detected defects over time, manufacturers can identify root causes of quality issues and implement long-term solutions to improve overall product quality.
RFID tags identifying inventory locations
Radio-Frequency Identification (RFID) technology has revolutionized inventory management in connected factories. RFID tags attached to raw materials, work-in-progress items, and finished products allow for real-time tracking of inventory as it moves through the production process.
This real-time inventory visibility enables more efficient resource allocation, reduces the risk of stockouts, and helps optimize the flow of materials through the factory. Additionally, RFID technology can improve traceability, allowing manufacturers to quickly locate specific items or batches if quality issues arise.
Automated control through machine learning algorithms
The true power of connected factories lies in their ability to not just collect and analyze data, but to act on it automatically. Machine learning algorithms play a pivotal role in this automated control, enabling factories to adapt and optimize their operations in real-time without human intervention.
Predictive maintenance models preventing downtime
One of the most impactful applications of machine learning in connected factories is predictive maintenance. By analyzing historical data and real-time sensor readings, these algorithms can predict when a machine is likely to fail with remarkable accuracy. This allows maintenance teams to schedule repairs during planned downtime, avoiding costly unplanned stoppages.
Predictive maintenance models continue to learn and improve over time, becoming more accurate as they process more data. This continuous improvement cycle ensures that factories become increasingly efficient at preventing downtime, leading to significant cost savings and improved productivity.
Dynamic scheduling optimizing resource allocation
Connected factories use machine learning algorithms to dynamically adjust production schedules based on a multitude of factors. These algorithms consider current inventory levels, incoming orders, machine availability, and even external factors like supplier delays or market demand fluctuations.
By continuously optimizing the production schedule, connected factories can maximize resource utilization, reduce waste, and improve delivery times. This dynamic approach to scheduling allows manufacturers to be more responsive to customer needs and market changes, giving them a competitive edge in fast-paced industries.
Anomaly detection identifying process deviations
Machine learning-powered anomaly detection systems act as vigilant overseers of the production process, constantly monitoring for any deviations from normal operations. These systems learn what "normal" looks like for each process and can quickly flag any unusual patterns or behaviors.
Anomaly detection can identify a wide range of issues, from subtle changes in product quality to potential safety hazards. By catching these deviations early, factories can address problems before they escalate, ensuring consistent product quality and maintaining a safe working environment.
Integration with enterprise software systems
For a connected factory to truly deliver on its promise of end-to-end optimization, it must seamlessly integrate with existing enterprise software systems. This integration creates a unified digital ecosystem that spans from the factory floor to the boardroom, enabling more informed decision-making at all levels of the organization.
Enterprise Resource Planning (ERP) systems, for instance, can be directly linked to the production data from the connected factory. This allows for real-time updates on inventory levels, production progress, and resource utilization. Such integration enables more accurate forecasting, better supply chain management, and improved financial planning.
Similarly, integration with Customer Relationship Management (CRM) systems can provide valuable insights into customer preferences and demand patterns. This information can be fed back into the production planning process, allowing manufacturers to align their output more closely with market needs.
Quality Management Systems (QMS) also benefit greatly from integration with connected factory data. Real-time quality metrics from the production line can be automatically fed into the QMS, enabling faster response to quality issues and more effective continuous improvement initiatives.
The key to successful integration lies in establishing standardized data formats and robust APIs that allow different systems to communicate effectively. Many connected factory solutions now come with pre-built integrations for common enterprise software, simplifying the process of creating a truly connected manufacturing ecosystem.
As connected factories continue to evolve, we can expect to see even deeper levels of integration, with artificial intelligence playing an increasingly important role in orchestrating the flow of information and decision-making across the entire manufacturing value chain. This holistic approach to manufacturing intelligence promises to unlock new levels of efficiency, agility, and innovation in the industrial sector.