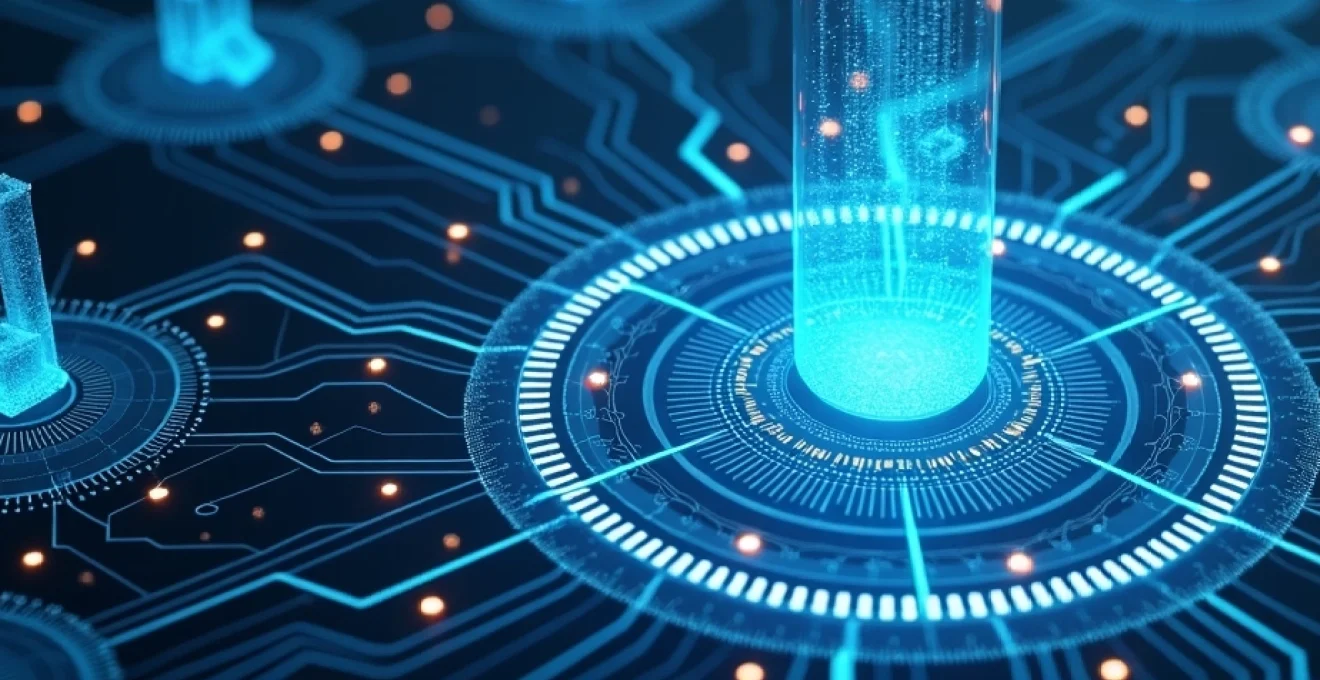
The manufacturing landscape is undergoing a seismic shift as Industry 4.0 technologies revolutionize traditional processes. This digital transformation is reshaping factories, supply chains, and workforce dynamics, promising unprecedented levels of efficiency, flexibility, and innovation. As smart factories emerge and data-driven decision-making becomes the norm, manufacturers must adapt to stay competitive in this new era of production.
Evolution of manufacturing: from traditional to industry 4.0
The journey from traditional manufacturing to Industry 4.0 represents a quantum leap in production capabilities. Traditional manufacturing relied heavily on manual labor, rigid production lines, and limited automation. In contrast, Industry 4.0 introduces a level of connectivity and intelligence that was previously unimaginable.
At the heart of this evolution is the concept of the "smart factory," where interconnected machines communicate in real-time, production processes self-optimize, and entire supply chains are integrated into a seamless digital ecosystem. This transformation is not just about technology; it's a fundamental reimagining of how products are designed, manufactured, and delivered to consumers.
The impact of Industry 4.0 on traditional manufacturing is profound. It's enabling manufacturers to move from mass production to mass customization, drastically reducing lead times and improving product quality. Moreover, it's creating new business models and revenue streams, as manufacturers can now offer data-driven services alongside their physical products.
Core technologies driving industry 4.0 transformation
Several key technologies are at the forefront of the Industry 4.0 revolution, each playing a crucial role in transforming traditional manufacturing processes. These technologies work in concert to create a more intelligent, flexible, and efficient manufacturing ecosystem.
Internet of Things (IoT) in smart factories
The Internet of Things (IoT) is the backbone of Industry 4.0, connecting machines, products, and systems in a vast network of sensors and devices. In smart factories, IoT enables real-time monitoring of production processes, predictive maintenance, and automated inventory management. This constant flow of data allows manufacturers to optimize operations, reduce downtime, and respond quickly to changes in demand or production conditions.
For example, sensors on production equipment can detect early signs of wear and tear, allowing maintenance to be scheduled before a breakdown occurs. This predictive approach can significantly reduce unplanned downtime and extend the lifespan of expensive machinery.
Big data analytics and machine learning applications
The vast amount of data generated by IoT devices in smart factories is only valuable if it can be effectively analyzed and acted upon. This is where big data analytics and machine learning come into play. These technologies can process enormous volumes of data to identify patterns, predict outcomes, and optimize processes in ways that human operators simply cannot match.
Machine learning algorithms can continuously analyze production data to identify inefficiencies, predict quality issues, and even suggest process improvements. This level of insight enables manufacturers to make data-driven decisions that can significantly improve productivity and product quality.
Cloud computing and edge processing in manufacturing
Cloud computing provides the scalable infrastructure needed to store and process the massive amounts of data generated in Industry 4.0 environments. It allows manufacturers to access powerful computing resources on-demand, without the need for significant upfront investment in IT infrastructure.
Edge computing, on the other hand, brings data processing closer to the source, reducing latency and enabling real-time decision-making. In manufacturing, this can be critical for applications that require immediate responses, such as safety systems or quality control checks.
Additive manufacturing and 3D printing advancements
Additive manufacturing, commonly known as 3D printing, is revolutionizing product development and production processes. It allows for rapid prototyping, the creation of complex geometries that were previously impossible to manufacture, and the production of customized parts on-demand.
In traditional manufacturing, creating a new product or part often required expensive tooling and long lead times. With 3D printing, manufacturers can produce small batches or even individual parts quickly and cost-effectively, opening up new possibilities for customization and reducing inventory costs.
Augmented reality (AR) for production and maintenance
Augmented Reality (AR) is transforming how workers interact with machines and perform maintenance tasks. By overlaying digital information onto the physical world, AR can provide workers with real-time instructions, highlight potential issues, and even guide them through complex procedures.
For instance, a maintenance technician wearing AR glasses could see step-by-step repair instructions overlaid directly on the machine they're working on, reducing errors and improving efficiency. Similarly, AR can be used in quality control processes, helping workers identify defects more accurately and consistently.
Digital twin technology in modern manufacturing
Digital twin technology is a game-changer for modern manufacturing, creating virtual replicas of physical assets, processes, or systems. These digital twins allow manufacturers to simulate, analyze, and optimize their operations in a risk-free virtual environment before implementing changes in the real world.
By continuously updating the digital twin with real-time data from its physical counterpart, manufacturers can gain unprecedented insights into their operations. This technology enables predictive maintenance, process optimization, and even the testing of new product designs without the need for physical prototypes.
For example, a car manufacturer could use a digital twin of their production line to simulate different configurations, identifying bottlenecks and optimizing throughput before making any physical changes. This approach can lead to significant cost savings and reduced downtime during upgrades or reconfigurations.
Cybersecurity challenges in connected industrial systems
As manufacturing systems become increasingly connected and reliant on digital technologies, cybersecurity has emerged as a critical concern. The potential for cyber attacks to disrupt production, steal intellectual property, or even compromise safety systems has made cybersecurity a top priority for Industry 4.0 implementations.
Traditional manufacturing environments were often isolated from external networks, providing a degree of inherent security. However, the interconnected nature of Industry 4.0 systems creates new vulnerabilities that must be addressed. Manufacturers must now consider cybersecurity at every level of their operations, from individual IoT devices to enterprise-wide systems.
Implementing robust cybersecurity measures requires a multi-layered approach, including:
- Secure network architectures with proper segmentation
- Regular security audits and vulnerability assessments
- Continuous monitoring for anomalies and potential threats
- Employee training on cybersecurity best practices
- Secure supply chain management to prevent upstream vulnerabilities
As cyber threats continue to evolve, manufacturers must remain vigilant and adapt their security strategies accordingly. This ongoing challenge requires collaboration between IT and OT (Operational Technology) teams, as well as partnerships with cybersecurity experts and technology providers.
Workforce transformation: skills for industry 4.0
The transition to Industry 4.0 is not just about technology; it's also about people. The skills required in modern manufacturing environments are evolving rapidly, creating both challenges and opportunities for the workforce. As automation takes over routine tasks, there's an increasing demand for workers with digital skills, problem-solving abilities, and the capacity to work alongside advanced technologies.
Reskilling programs for traditional manufacturing workers
To address the skills gap created by Industry 4.0, many manufacturers are investing heavily in reskilling programs for their existing workforce. These programs aim to equip traditional manufacturing workers with the digital skills needed to operate and maintain advanced manufacturing systems.
Reskilling initiatives often focus on areas such as data analysis, programming, and system integration. By providing employees with these new skills, manufacturers can retain valuable institutional knowledge while adapting to new technologies.
Emerging roles: data scientists and IoT specialists in factories
The rise of Industry 4.0 has created demand for entirely new roles within manufacturing organizations. Data scientists, for example, are now crucial in helping manufacturers make sense of the vast amounts of data generated by smart factories. IoT specialists are needed to design, implement, and maintain the complex networks of connected devices that form the backbone of Industry 4.0 systems.
These new roles require a blend of technical skills and domain-specific manufacturing knowledge, creating opportunities for both new entrants to the industry and experienced manufacturing professionals who are willing to adapt and learn.
Human-robot collaboration and cobot integration
As robots become more advanced and capable of working safely alongside humans, the concept of human-robot collaboration is gaining traction in manufacturing environments. Collaborative robots, or "cobots," are designed to work in close proximity to human workers, augmenting their capabilities rather than replacing them entirely.
This shift requires workers to develop new skills in robot programming, operation, and maintenance. It also demands a change in mindset, as employees learn to view robots as tools to enhance their productivity rather than as threats to their jobs.
Virtual and Augmented Reality training platforms
Virtual and Augmented Reality (VR/AR) technologies are revolutionizing how manufacturers train their workforce. These immersive technologies allow workers to practice complex procedures in a safe, virtual environment before performing them on actual equipment.
VR/AR training platforms can simulate a wide range of scenarios, from routine maintenance tasks to emergency procedures, providing workers with hands-on experience without the risk of costly mistakes or safety hazards. This approach can significantly reduce training time and costs while improving knowledge retention and performance.
Case studies: successful industry 4.0 implementations
To illustrate the real-world impact of Industry 4.0, let's examine some successful implementations across various manufacturing sectors.
Siemens' Amberg electronics plant
Siemens' Amberg Electronics Plant in Germany is often cited as a prime example of Industry 4.0 in action. The facility produces programmable logic controllers (PLCs) with a remarkable degree of automation and efficiency. Over 75% of the value chain is automated, with machines and computers handling 50 million process-related data transactions daily.
The plant uses digital twins to simulate and optimize production processes, resulting in a defect rate of less than 12 parts per million. This level of quality and efficiency demonstrates the potential of Industry 4.0 technologies when fully integrated into manufacturing operations.
Bosch Rexroth's multi-product line in Homburg
Bosch Rexroth's plant in Homburg, Germany, showcases the flexibility and customization capabilities of Industry 4.0. The facility features a multi-product line that can produce over 200 different hydraulic valves on the same equipment without requiring retooling.
This is achieved through the use of RFID-tagged workpieces that carry their own production instructions, allowing machines to automatically adjust their operations for each individual product. The result is a highly flexible production system that can efficiently handle small batch sizes and custom orders.
Tesla's Gigafactory: advanced automation and AI
Tesla's Gigafactory represents a bold vision for the future of automotive manufacturing. The facility leverages advanced automation and artificial intelligence to produce electric vehicles and battery packs at unprecedented scale and efficiency.
One of the key innovations at the Gigafactory is the use of AI-powered quality control systems. These systems use computer vision and machine learning to inspect components and finished products with a level of precision and consistency that surpasses human capabilities. This approach has allowed Tesla to maintain high quality standards while rapidly scaling up production.
Basf's smart manufacturing in Ludwigshafen
BASF, the world's largest chemical producer, has implemented Industry 4.0 technologies at its massive Ludwigshafen site in Germany. The company uses advanced analytics and machine learning to optimize its complex production processes, resulting in significant energy savings and increased efficiency.
One notable application is the use of AI to predict and prevent equipment failures. By analyzing data from thousands of sensors across the plant, BASF can identify potential issues before they cause disruptions, reducing downtime and maintenance costs.
These case studies demonstrate that Industry 4.0 is not just a theoretical concept, but a practical reality that is already delivering tangible benefits across diverse manufacturing sectors. As more companies embrace these technologies, we can expect to see continued innovation and transformation in the manufacturing landscape.